Procedure to approval plastics
Procedure to approval plastics
How is the procedure to approve plastics like?
It is a completely outsourced and transparent process consisting of passing an audit, which observes fundamental aspects in any industrial activity in the industry, grouped in the following modules:
-
Administrative documentation
-
Environmental and quality management
-
Technological capacity and quality of finished product
-
Processing capacity and traceability
Approval conditions
For the approval process, it is necessary to have a working facility, since part of the process consists of doing an industrial test in the facility, to measure the annual processing capacity (tonnes/year).
The final products required following the processing are, at least, the following products, according to type of material:
Clean scale.
Pellet.
Pellet.
Its traceability must be ensured at all times during the process polypropylene and polystyrene pellets (separately). During the approval process, in the event that, in the curse of the industrial test to determine the treatment capacity, the approval audit team verifies the inability of the facility to reach the productive capacity, the capacity may be verified through the technical documentation of the machines. In this regard, the recycler must, at least, sort the two materials separately, polystyrene and polypropylene, and granulate the majority, being able to establish the treatment capacity of the minority material through the procedure indicated above.
When an approved recycler for the Mixed plastic material (Current TSRM) receives material allocated to it by Ecoembes, it will have two options:
- Option 1: Granulate, separately and in its approved facilities, each of the two fractions (polypropylene and polystyrene).
- Option 2: Granulate only one of the two fractions (polypropylene or polystyrene) in its approved facility, as long as it guarantees the recycling of the other fraction in another facility.
Polypropylene and polystyrene pellets (separately). During the approval process, in the event that, in the curse of the industrial test to determine the treatment capacity, the approval audit team verifies the inability of the facility to reach the productive capacity, the capacity may be verified through the technical documentation of the machines. In this regard, the recycler must, at least, sort the two materials separately, polystyrene and polypropylene, and granulate the majority, being able to establish the treatment capacity of the minority material through the procedure indicated above.
When an approved recycler for the Polypropylene + Polystyrene material receives material allocated to it by Ecoembes, it will have two options:
- Option 1: Granulate, separately and in its approved facilities, each of the two fractions (polypropylene and polystyrene).
- Option 2: Granulate only one of the two fractions (polypropylene or polystyrene) in its approved facility, as long as it guarantees the recycling of the other fraction in another facility.
Granza.
* Mixed plastic and Polypropylene + Polystyrene (PP+PS) only in the case of light packaging sorting plants (certification is not required for mass waste plants, since Ecoembes does not market packaging for these fractions).
** Polypropylene (PP) only in the case of mass garbage plants.
Approval is a requirement to opt for Ecoembes’ offers, but being approved does not ensure supplying the material.
The approval of Plastic Mixture enables participation in the awards for the Plastic Mixture (Current ETMR) and Plastic Mixture (Future ETMR) fractions.
Steps in the process
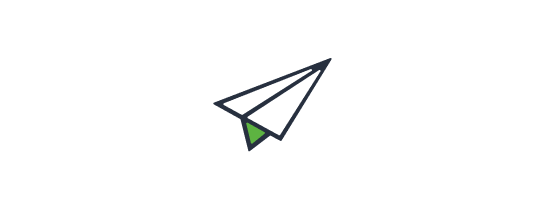
1. Sending the application
1. Sending the application
The companies interested in the approval must fill in the form (spanish version) with their details.
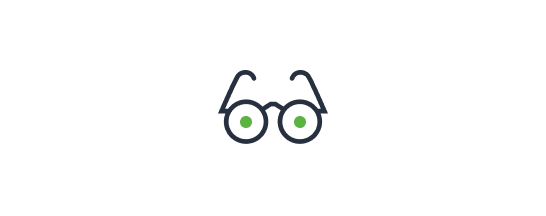
2. Audit
2. Audit
The audit costs are borne by the applicant interested in the approval.
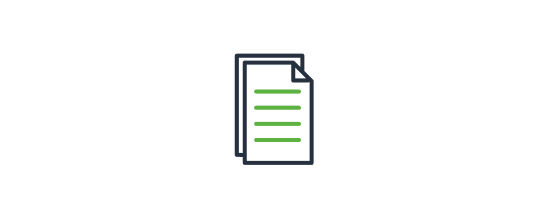
3. Report
3. Report
The report includes all the aspects foreseen in the reference standard.
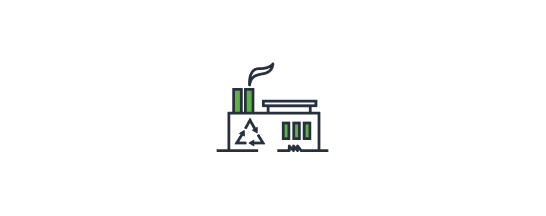
4. Inclusion of the company
4. Inclusion of the company
If the company is approved, it becomes part of the “Approved Recovery/Recycling Agents List” on Ecoembes’ website. The certification issued to each recycler will be valid for a maximum of eight (8) years, although it will be tied to the validity of the corresponding administrative authorization to collect and treat waste provided for in Article 33 of Law 7/2022 of April 8, on waste and contaminated soils for a circular economy, or any law that may replace it. For example, if a recycler requests certification from ECOEMBES in the fourth year of validity of its administrative authorization, its certification will be valid for four years.